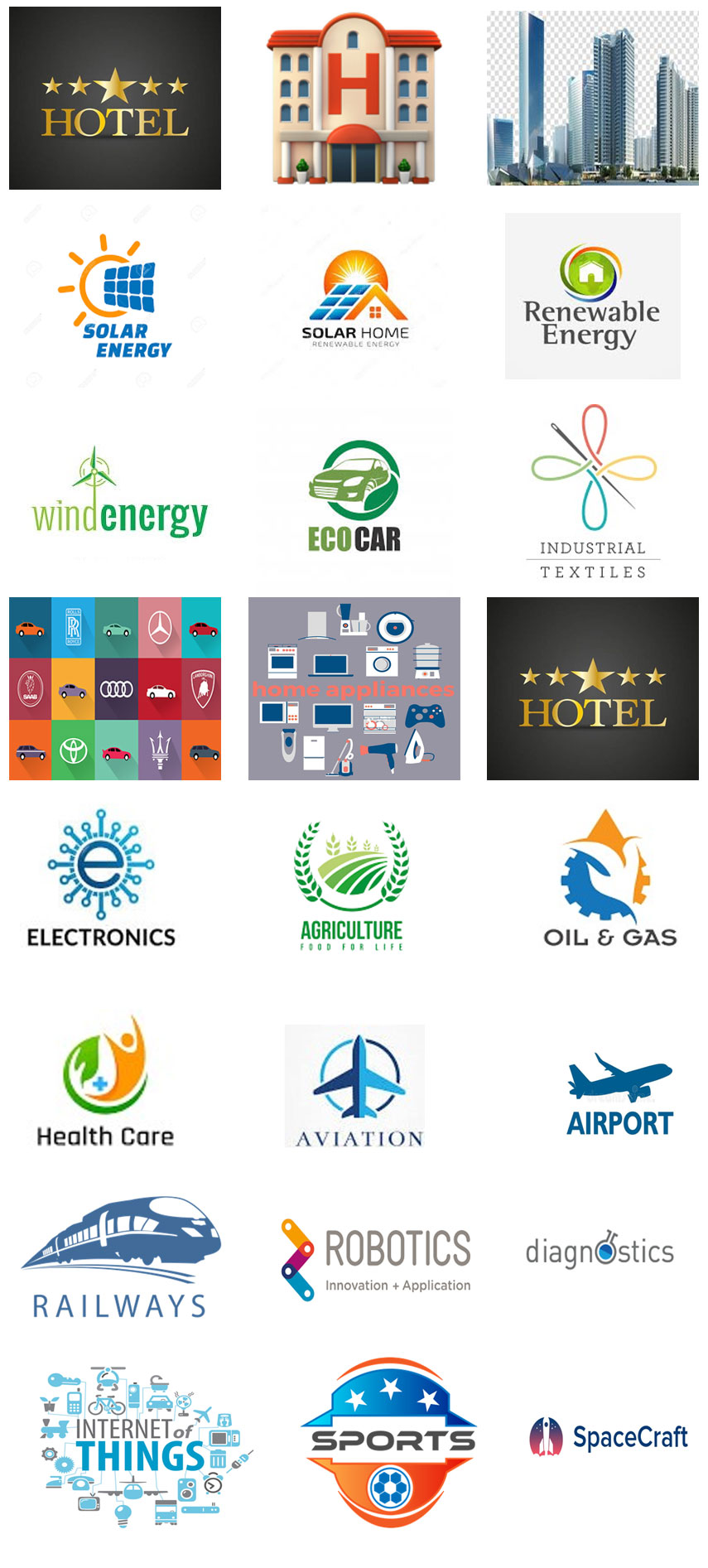
***** Hotel industry challenges
•Metal Rusting, Corrosion, Oxidation
•Metal SS elevators deep scratches on matt or mirror finish
•Contaminated embedded hard water marks/lime scaling/ acid frostiness/ cement stains / iron mist on Glass
•Scratched Glasses, Metals, SS areas
•Algae / Fungus on Glass, Marble, Metal etc
•Scraper to remove acidic bird droppings on Glass leads to scratches.
•Glass absorbs light making inefficient R.A.C unit with increased electricity costs.
•Glass skylights/facades absorbing sunlight with heat insulation in internal buildings.
•Daily / regular cleaning or maintenance done on Glass, Metal, Marble by hotel staff wastes time, energy, resources, water
•External Glass facades or areas are exposed to pollution that damages the surface leading to expenses
•During rainfall season, the contaminants get stuck on the external Glass or other surfaces
•Glass condensation issues due to outside humidity & temperature difference obscures the view of the hotel guests and damages glass as the moisture hits the glass
•Usage of current acidic / alkaline cleaning chemicals damages the glass, metal , makes the skin dry and itchy, health is at risk
•Glass having protective plastic film is difficult to maintain or clean, also leads to fungus or hard water marks formation.
•Usage of tinted glass obscures view, reduces solar heat gain.
•Hospitality laundry industry deals with 4 to 10 tonnes of clothes daily releasing dirty water in ETP plant to purify it, before exposing to environment.
•Contamination of other metal surfaces like MS, aluminium, cast Iron, or other surfaces like ceramic, porcelain, marble, granite, tiles, terracotta, fabric, polishes concrete, stone, sandstone, limestone, wood, textile, solar panels etc
Our Nanotechnology solutions for ***** Hotel
•Anti corrosion long lasting nanocoating
•Restoration of scratches on metal SS elevators, & nanocoating
•Eco-friendly turn key solution from Glass restoration, super hydrophobic nano coating with mercury effect
•Scratches removal with scratch resistance
•Anti-bacterial / fungal Glass, Marble, Metal etc
•Nano coating with photocatalytic effect decomposes acidic bird droppings, avoids yellow mark, avoids scraper usage.
• Nanocoating has UV protection barrier, conserves A.C load and reduces electricity costs.
•Nano composite reflects sunlight up to 90%, with summer n winter benefit, solves heat solution
•Self cleaning super hydrophobic nano coating helps in reducing the maintenance and saves time, energy, resources
•Reduces pollution & cleans air as nanocoating decomposes toxic organic substances, protecting Glass surfaces
•Nanocoating has a water sheathing effect, contaminants gets washed away by rainfall water.
•Glass nano coating helps in solving condensation to a certain extent that it prevents water from creating any permanent glass damage & does not obscure the guests view.
•Our eco-friendly nanocoating is neither acidic nor alkaline, thus glass, metal, other surfaces and humans are all safe.
•Our turn key restoration nanocoating solutions maintains and restores the filmed glass easily.
•Nanocoating does not obscure the view as its invisible.
•Nano washing solution usage avoids ETP process, is eco-friendly, no harmful chemicals phosphorous, boron, benzyl acetate, C7H8O.
•Restoration & nanocoating of other metal surfaces like MS, aluminium, cast iron, or other surfaces like ceramic, porcelain, marble, granite, tiles, terracotta, fabric, polishes concrete, stone, sandstone, limestone, wood, textile, solar.
Real estate / skyscrapers/ buildings industry challenges
•Metal Rusting, Corrosion, Oxidation
•Metal SS elevators deep scratches on matt or mirror finish
•Contaminated embedded hard water marks/lime scaling/ acid frostiness/ cement stains / iron mist on Glass
•Scratched Glasses, Metals, SS areas
•Algae / Fungus on Glass, Marble, Metal etc
•Scraper to remove acidic bird droppings on Glass leads to scratches.
•Glass absorbs light making inefficient R.A.C unit with increased electricity costs.
•Glass skylights/facades absorbing sunlight with heat insulation in internal buildings.
•Daily / regular cleaning or maintenance done on Glass, Metal, Marble by staff wastes time, energy, resources, water
•External Glass facades or areas are exposed to pollution that damages the surface leading to expenses
•During rainfall season, the contaminants get stuck on the external Glass or other surfaces
•Glass condensation issues due to outside humidity & temperature difference obscures the view of the guests and damages glass as the moisture hits the glass
•Usage of current acidic / alkaline cleaning chemicals damages the glass, metal , makes the skin dry and itchy, health is at risk
•Glass having protective plastic film is difficult to maintain or clean, also leads to fungus or hard water marks formation.
•Usage of tinted glass obscures view, reduces solar heat gain
•Heat insulation issues of buildings leading to discomfort of humans, inefficient AC leading to high electricity costs.
•Contamination of other metal surfaces like MS, aluminium, cast Iron, or other surfaces like ceramic, porcelain, marble, granite, tiles, terracotta, fabric, polishes concrete, stone, sandstone, limestone, wood, textile, solar panels etc
Our Nanotechnology solutions for Real estate
•Anti corrosion long lasting nanocoating
•Restoration of scratches on metal SS elevators, & nanocoating
•Eco-friendly turn key solution from Glass restoration, super hydrophobic nano coating with mercury effect
•Scratches removal with scratch resistance
•Anti-bacterial / fungal Glass, Marble, Metal etc
•Nano coating with photocatalytic effect decomposes acidic bird droppings, avoids yellow mark, avoids scraper usage.
• Nanocoating has UV protection barrier, conserves A.C load and reduces electricity costs.
•Nano composite reflects sunlight up to 90%, with summer n winter benefit, solves heat solution
•Self cleaning super hydrophobic nano coating helps in reducing the maintenance and saves time, energy, resources
•Reduces pollution & cleans air as nanocoating decomposes toxic organic substances, protecting Glass surfaces
•Nanocoating has a water sheathing effect, contaminants gets washed away by rainfall water.
•Glass nano coating helps in solving condensation to a certain extent that it prevents water from creating any permanent glass damage & does not obscure the guests view.
•Our eco-friendly nanocoating is neither acidic nor alkaline, thus glass, metal, other surfaces and humans are all safe.
•Our turn key restoration nanocoating solutions maintains and restores the filmed glass easily.
•Nanocoating does not obscure the view as its invisible
•Nanocomposite, nano porous gels & foams(aerogels & polymer foams for thermal insulation solutions.
•Restoration & nanocoating of other metal surfaces like MS, aluminium, cast iron, or other surfaces like ceramic, porcelain, marble, granite, tiles, terracotta, fabric, polishes concrete, stone, sandstone, limestone, wood, textile, solar.
Renewable / Solar Energy industry challenges
•Solar panels inefficiency in solar energy capture, according to national academy engineering is only 10 to 20% efficiency
•Contamination on solar panels like bird droppings, pollution, dust, hard water marks, lime scaling etc
•Contamination leads to permanent solar panels damage with heavy dust accumulation & poor solar panel performance.
•Solar cells panels being outside are prone to becoming very dirty, with layer of dirt masking the catalytic areas of solar cells, thus reducing their efficiency & lifetime, adds global warming.
•Cleaning & maintaining dirty solar panels with commercial detergents or chemicals is time consuming, costly, hazardous
•To maintain solar panels peak efficiency it is required to clean every few weeks which is hard for large solar panel array.
•Increase of energy demand by CO2 neutral renewable energy source like solar energy is rising due to population & economy.
•Capital cost for solar energy PV photovoltaic system is high, thus drop in solar energy efficiency is not desired.
•Consumption of solar energy delivered by sun is only a fraction, leaving the rest of the immense high potential solar energy.
•Every day earth is hit by 165000 TW solar power with inefficient solar energy collection, conversion, storage etc.
•Solar sunrays transmission through the panels is very average, with loss in power output of solar PV.
•Solar cells does not effectively reduce the reflectance of the solar cells across the near UV to near IR spectral range, thus no improvement in the output power.
•Current technology cannot be applied on all types of solar panels, i.e. installed and non installed.
•Current technology are not durable or long lasting.
•Current tech is not eco friendly or reducing caron footprint.
•Current tech does not have anti bacterial photocatalytic effect, does not decompose acidic bird droppings, with yellow marks.
•Conventional coatings do not have superior characteristics: it does not reduce surface roughness for better dirt repellence, does not minimize moisture penetration, water adheres.
•Solar panels may initiate fogging up when in contact with steam or condensation.
Our Nanotechnology solutions for Solar Energy industry
•Solar Nanocoating boost solar energy capture, absorbs more sunlight than uncoated solar panels
•Restoration of all contamination as well as nano coating that prevents future contamination on solar panels
•Solar anti-soil nanocoating effect prevents solar panels permanent damage, very low dust easily cleaned by rainwater.
•Solar nanocoating is superhydrophobic with mercury effect makes panel cleaner & transparent to UV light, thus increasing efficiency, durability & lifetime, prevents global warming.
•Self cleaning nanocoating for solar panels enhances efficiency as well as saves maintenance cost and saves time & energy
•Nanocoating repels dust, pollen & other particles to keep solar panels clean to operate at their peak efficiency.
•Solar Nanocoating helps in meeting the increase in energy demand expected from concentrating solar energy.
•Solar nanocoating is very cost effective maintenance for a high capital intensive PV solar system to enhance its efficiency.
•Solar nanocoating makes the maximum utilization of solar energy resources which is clean & sustainable.
•Solar nanocoating can help the future need of solar PV cells with conversion efficiencies of 45% vis a vis current of 15/20%.
•Nanocoating on solar glass increases the transmission of up to 96%, thus raises solar power efficiency. & power output of PV.
•Solar nanocoating reduces reflectance of solar cells by approx. 10% across near UV to near IR spectral range, thus with 17% increase in output power. Quantum dots, wires by over 60%.
•Solar nanocoating technology can be applied on all types of solar panels, i.e. installed as well as non installed.
•Solar nanocoating is durable, long lasting, easy to apply.
•Solar nanocoating is eco friendly reducing carbon footprint
•Solar nanocoating has anti bacterial photocatalytic effect decomposing harmful acidic bid droppings automatically.
•Solar nanocoating has superior characteristics: it reduces surface roughness to 1 nm for better dirt repellence, minimizes moisture penetration, water repels.
Solar superhydrophobic nanocoating prevents fogging up when in contact with steam or condensation
Wind Energy / Renewable Energy challenges
•Inefficient & heavy rotor blades of wind & tide power plants, wear and tear, corrosion.
•Demand of high energy output & low carbon footprint, for bigger wind turbine blades in multimegawatt projects, not met.
•Wind turbine blade cycle lifetime in the wind energy value chain is not that big.
•Weight of the wind turbine blades should not be more, even when there is demand of wind blade length to be increased.
•Wind energy capture in current wind energy offshore and onshore megawatt projects are not efficient.
•Wind energy rotor blades are heavy weight & of low strength,decreases the wind energy conversion efficiency
•Maximum use of wind energy not achieved, despite being a clean fuel renewable energy source not emitting atmospheric emissions causing acid rain, smog, greenhouse gases.
•Good land-based wind sites are often located in remote locations, far from cities where the electricity is needed.
•Wind energy distribution is not efficient leading to low voltage power transmission & loss and inefficient wire based less conducting power lines.
•Higher wind power plant efficiencies require higher operating temperatures and thus heat-resistant turbine materials.
•High loss power transmission & inefficient smart grids, in wind energy distribution.
•Harnessed wind energy power is stored in inefficient batteries or supercapacitors.
•Wind power plants bearings and gear boxes are not protected, no protection from lightning, high cost energy storage when wind energy is harnessed, thus leading to expensive feeding of wind power in the grid.
•Wind power plants generate noise pollution in nearby areas with rotor blades moving at speed , increasing noise level of wind generators & leading to inefficient wind energy.
Our Nanotechnology solutions for Wind Energy industry
•Nanomaterials lead to lighter &rugged rotor blades, wear & corrosion protection nanocoatings for bearings & powertrains.
•Demand can be met by increase in wind blade length & enhanced functional properties with nano enabled components
•Wind cycle blade cycle lifetime can be increased by use of nano coatings and nano paints.
•Weight of the wind turbine blades can be reduced by using nano-based prepregs even in lengthy wind blades.
•Wind energy capture efficiency can be increased by use of nano lubricants, nanofluids, nano enabled wires and cables.
•Structural nanocomposites in rotor blades with carbon based materials like nanotubes makes it lighter & stronger & rugged.
•Nanotechnology can help achieve the maximum use of wind energy as it is most effective renewable energy source as well as most sustainable and easily available source.
•Nanotechnology can help in building effective & fast transmission lines to bring electricity from wind farm to city.
•Nanofillers & soft magnetic nanomaterials helps in high voltage power transmission & nano superconductors for loss less transmission, superconducting CNT power lines, wireless.
•Nano-scale heat &corrosion protection layers for turbine blades in power plants to enhance efficiency.
•CNT nanomaterials can help in loss less power transmission & efficient smart grids in wind energy distribution.
•Nanotechnology improves capacity & safety of Li-ion batteries via new ceramic, heat resistant & still flexible separators.
•Tribological nano coatings & wear protection layers of bearings & gear boxes, CNT conductive nanomaterials for protection against lightning strikes or nano-optimized energy stores for economic feeding of wind power in the grid.
•Nano structuring processes uses biomimetic effect that counteracts eddies development at rotor vanes, thus reducing noise level of wind generators & optimize energy.
•According to estimations by Cientifica, nanotechnologies will tap the greatest market potentials in the field of energy savings with approx. 40 bn $ in the short to medium run, inter alia in the following fields of application.
Aviation
Nanomaterials are used in aircrafts as a substitute of conventional composites to help reduce aircraft weight, saving thousands of tons of fuel
Oil and Gas industry challenges
Oil and Gas industry faces multiple challenges like inefficient or loss of Oil while Oil Water separation, inefficient Co2 –N2 separation, existing toxic metals, inefficient oil exploration and recovery and expensive oil production processes. Current materials lead to inefficient gas separation and thereby existing impurities in oil.
Connecting one pipe to another in the lengthy pipeline, the connecting areas have connecting joints by bolts and nuts get exposed to corrosion and rusting. Storage barrels & Gas gallons transporting equipment's to reach gas stations are corroded.
Current particles used have inefficient properties for measuring and imaging for oil exploration and inefficient fluid flow monitoring. There is an unnecessary fluid loss and poor wellbore stability which leads to thick filter cake and differential pressure sticking problem and leads to damage while drilling.
There is a significant frictional resistance between the pipe and borehole wall which leads to torque and drag problems of horizontal, extended reach and multilateral and coiled tubing drilling, that leads to major energy loss by frictional energy loss that is caused by the viscous effects of the fluid and & pipe wall roughness.
Hydrogen sulfide is a very dangerous, toxic and corrosive gas. It can diffuse into drilling fluid from formations during drilling of gas and oil wells. Hydrogen sulfide should be removed from the mud as it leads to the environmental pollution, spoils the health of drilling workers and leads to corrosion of pipelines and equipment.
Toxic Gases and substances are harmful to environment and not removed efficiently by other processes. Nitrogen oxides, sulfur oxides, acids etc are harmful.
Heavy Oil is very viscous and thus this high viscosity leads to many challenges like very slow and inefficient fluid flow in the pipeline and thereby high operations costs.
Acid solutions are pumped for acid cleaning, acidizing, descaling and oil well cleaning, etc. For most of these operations, the acids are transported through metallic conduits, thereby exposing these metallic surfaces to chemical reactions that corrode them
Oil and Gas industry Nanotechnology solutions
Oil and Gas Nanotechnology advantages: efficient Oil Water separation, Co2 – N2 separation, toxic metal removal, increased oil exploration and recovery, eliminate cost of oil production by eliminating challenges. New gen nanomembranes help in enhanced separation of gas streams and removal of impurities from oil.
Our Nano-coating prevents the corrosion and rusting in the connecting areas of the lengthy pipeline and also around the internal pipelines areas. Also, storage barrels can go for our nanocoating. Gas gallons transporting equipment’s can prevent corrosion with our nano-coating.
Nanoparticles with better optical, magnetic, electrical properties are innovative and novel for measuring and imaging with better resolution for oil exploration and effective fluid flow monitoring.Nanoparticles used as drilling fluid additives to reduce the fluid loss and enhance the wellbore stability. The filter cake is thin, helps for reducing the differential pressure sticking problem and prevents damage while drilling.
Our Nano coating , due to fine and very thin film forming capability of nanomaterials, nano-based fluids can provide a significant reduction of the frictional resistance between the pipe and the borehole wall due to the formation of a continuous and thin lubricating film in the wall-pipe interface, that smoothens the pipe wall and prevents its roughness allowing smooth fluid flow.
Removal of Toxic Gases:. synthesized zinc oxide nanoparticles are completely able to remove hydrogen sulfide from water based drilling mud in about 15 min., whereas bulk zinc oxide is able to remove 2.5% of hydrogen sulfide in as long as 90 min. under the same operating conditions. Thus, it helps in saving environment from pollution, protecting health of drilling workers and prevents pipeline corrosion.
Nano-filters and particles have the ability to efficiently remove harmful toxic substances such as nitrogen oxides, sulfur oxides, and related acids and acid anhydrides from vapor, and mercury from soil and water.
Nano particles due to its better viscous properties, reduces the viscosity of the oil and thus the less viscous oil flows fast and efficient fluid flow in the pipeline and thereby low operations costs.
Nanoparticles reduce corrosion rate of carbon steel in acidic medium. It acts as a corrosion inhibitor to minimize destructive effect.
Oil and Gas Industry challenges
High Temperature and High Pressure (HTHP) Challenges: In high temperature and high pressure drilling (HTHP) operations, usual drilling fluid systems have relatively poor heat transfer coefficient. The cooling efficiency of the traditional drilling fluids decreases due to slow dissipation of heat from the surfaces of down hole tools and equipment. Hence, there is a higher scope of equipment failure due to thermal degradation effect of high temperature.
The down hole tools and equipment are always exposed to abrasive forces due to high kinetic energy associated with the particles present naturally in the subsurface formations and the drill solids added to the drilling fluid system for specific functions. These forces cause the wear and the tear for most of the down hole equipment, especially in deviated and horizontal wells where the tools are more exposed to these abrasive forces.
In case of challenging drilling operations, deep water drilling or harsher conditions are met and the need for effective drilling bits increases due to inefficient drilling conditions and processes. PDC cutters for drill bits are not that effective in drilling process and the output is not that satisfying and the materials do not homogeneously integrate into the PDC synthesis.
Current materials used are heavier and of less strength. Current coatings do not have appropriate properties for long lasting effect and neither they add any environment value due to their acidic or alkaline nature and they do not help in the disintegration process. Thus, they lead to inefficient drilling and fluid flow .
Traditional light weight material for ball or plug applications are prone to early yielding or shape changes. The yield strength of conventional aluminium alloys is less than 400 Mpa. Severe deformation of currently used materials that prevent flow back, which requires costly operations to either remove or replace the tools, resulting in higher operational inefficiency.
Upgrading of bitumen and heavy crude oil has been another important challenge. Because of their high density and viscosity, it is difficult to handle and transport these chemicals to locations where they can be converted into valuable products.
Oil and Gas Industry Nanotechnology solutions
The extremely high surface area to volume ratio of nanoparticles enhances the thermal conductivity of Nano-based drilling fluids which provides efficient cooling of drill bit leading to a significant increase in operating life cycle of a drill bit, There is high heat tolerance,
high thermal conductivity, high mobility, effective interaction with external and internal rock surfaces, nano-based drilling mud systems are helpful in complex HTHP drilling operations,.
Increase down hole tools life: Because of their extremely small size, nanoparticles are preferred to be used in drilling fluid design as their abrasive forces are negligible with less kinetic energy impact. It is safer & eco-friendly. The nanoparticles are added to mud in small amount, with low concentration about 1%. So, Nano-based drilling fluids could be the fluid of choice in conducting drilling operations in sensitive environments to protect other natural resources.
Nano diamond PDC Technology: Carbon nanomaterials help due to their unique combination of technical, structural, electrical & thermal properties. Polycrystalline diamond applications like polycrystalline diamond compact (PDC) cutters for drill bits. They give PDC cutters unique surface characteristics that allow them to integrate homogeneously into PDC synthesis.
Using controlled electrolytic metallic (CEM) nanostructured material that is lighter than aluminium and stronger than some mild steels, but disintegrates when it is exposed to the appropriate fluid. The nanomatrix of the material is high strength and has unique chemical properties that conventional materials do not
Flow control and Completion devices such as fracturing balls, discs, and plugs are used for sleeve actuation or stimulation diversion during fracturing. The yield strength of nanomaterials is better, allowing stability of shape for smooth fluid flow, with cost effective operations as there is no need to remove or replace tools .
Nano-catalysts offer a solution for on-site upgrading of bitumen and heavy crude oil. Specifically designed nanocatalysts for on-site field upgrading combined with hydrogen/methane production
Oil and Gas industry challenges
Cementing problems in gas wells: Cement dehydration, decrease in compressive strength, leads to fluid loss, high probability of casing collapse leading to gas migration. Fungus or bacteria or algae growth, high maintenance costs, thermal shocks leading to cracks and high operations and replacement costs.
The current materials used leads to poor thermal or electrical conductivity, inefficient permeability / porosity, reduces mechanical properties and thereby leads to thermal operations damage and high operations and replacement costs.
Problems such as channelling, behind casing, contamination of surrounding aquifer, zonal isolation problems, cement setting time problems, etc. result from the use of convectional spacers. To avoid this contamination there is a need of nano spacers.
Recovery of gas from hydrates requires the dissociation of gas hydrate in three ways: thermal recovery, depressurization or by chemical inhibition. But, the problems associated are: Most chemical additives (salt, methanol, and glycol) cause pipe and equipment corrosion, ecological problems. Preheated gas or liquid transportation down to hydrate zone is accompanied by extensive heat loss. Microwave or electromagnetic method also requires vast energy transfer to decomposition zone and is inefficient.
High-molecular-weight cross-linked polymer fluids have been used to
stimulate oil and gas wells for decades. These fluids exhibit exceptional viscosity, thermal stability, proppant transportability, and fluid leak-off control. major drawback is the amount of polymer residue they leave behind. Polymer residue has been shown to significantly damage formation permeability and fracture conductivity.
Recently, viscoelastic surfactant (VES) fluids composed of low-molecular-weight surfactants have been used as hydraulic fracturing and frac-packing fluids. VES fluids, once broken, leave very little residue or production damage. However, excessive fluid leak-off & poor thermal stability has significantly limited their use.
Oil and Gas Industry Nanotechnology solutions
Enhancing Cement Properties: Due to the very high surface area of nanomaterials, they are used in oil well cementing to accelerate the cement hydration process, increase compressive strength, help control fluid loss, reduce probability of casing collapse & prevent gas migration, antibacterial, absorbs thermal shocks & prevent cracks.
Types of nanomaterials to be used in the oil well cementing industry: potential accelerators, nanomaterials to enhance mechanical properties, nanomaterials to reduce permeability/porosity, nanomaterials to increase thermal and or electrical conductivity.
Cement nano spacers formed by nano-emulsions can effectively clean OBM Oil based mud, from casing-wellbore surface during cementing job, and also, reverse the wettability of this surface to facilitate the adhesion of cement slurry between the casing and the open hole.
Injection of air-suspended self-heating nanoparticles in the hydrate formation through horizontal well, will penetrate deep into hydrate reservoir by passing through the cavities. These particles cause a temperature rise up to 42 0C in formation leading to disturbance in thermodynamic equilibrium and causing the water cage to decompose and release methane. The pressure of the fluids in contact with hydrate is lowered, pushing the hydrate out of its stability region and leading to its decomposition.
The nanoparticles have displayed unusual surface morphologies and have high
surface reactivity. These nanoscale particles, through chemisorption and surface charge attraction, associate with VES micelles to: 1) stabilize fluid viscosity at high temperatures; and 2) produce a pseudo filter cake of viscous VES fluid that significantly reduces the rate of fluid loss and improves fluid efficiency.
When internal breakers are used to break the VES micelles, the fluid will dramatically lose its viscosity and the pseudo-filter cake will then break into nanosized particles. Since the particles are small enough to pass through the pore throat of producing formations, they will be flowed back with the producing fluids, and no damage will be generated.
The observed challenges associated with the use of nanoparticles are their stability in a liquid medium and transportability in reservoir rocks. The addition of viscosifier was implemented by researchers to ensure stability, and also, they used surface-treated nanoparticles to facilitate stability and transportability.
Cement
In the application of cement, savings in raw materials of approx. 60 % and in CO2-emissions of approx. 40 % would be principally possible through nanooptimized ultra-high performance concrete with 10 times the strength of standard concrete, since much less material is required to fulfill the same mechanical demands